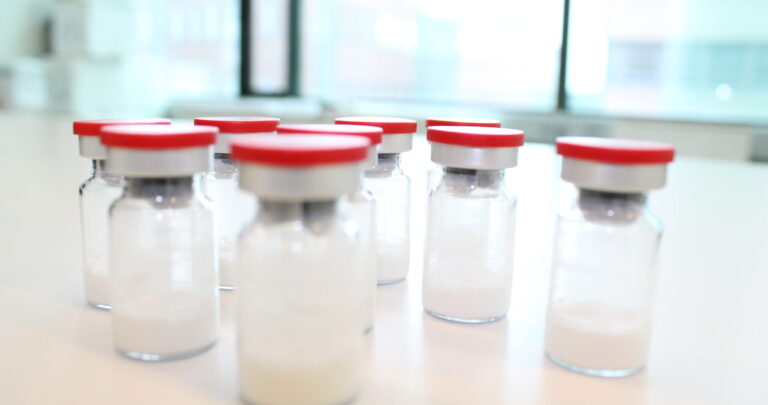
Headspace moisture determination
Analyzing residual moisture content with headspace analysis is….
- Rapid and non-destructive
- Capable of providing deep insight into efficiency of freeze drying processes
- Possible on 100% of the samples
- Preventing release of out of specification product
Residual moisture content is a critical parameter when considering the efficacy and shelf life of lyophilized pharmaceutical product. To specify and control the maximum allowable moisture content, analysis is carried out in product and process development as well as in commercial manufacturing.
Traditionally moisture content is determined using Karl Fischer titration or thermo-gravimetric analysis – which are not only destructive but also time and labor intensive methods. LIGHTHOUSE headspace moisture determination replaces these traditional destructive methods, to generate more and better data, faster.
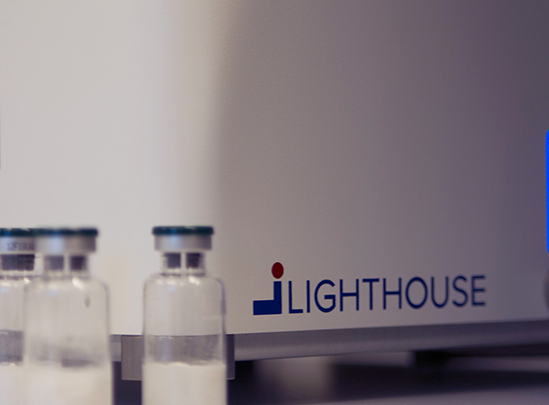
Prevent product degradation from moisture through robust package development and stability studies
To prevent moisture degradation, dry pharmaceutical products are sealed under an atmosphere of dry nitrogen or air. However, over the shelf life of the product moisture will permeate into the vial. The rate at which this happens can be monitored during stability using non-destructive headspace moisture analysis. In addition, package development studies can be carried out using the same technology to determine the best possible package components for your product.
![Compliance-Program-for-EU-Annex-1-Container-Closure-Requirements-1920×1080 [REVISED]](https://lighthouse.troop.dev/wp-content/uploads/2024/06/Compliance-Program-for-EU-Annex-1-Container-Closure-Requirements-1920x1080-REVISED-768x405.jpg)
Optimize your freeze drying process with 100% moisture mapping
Residual moisture levels of dry pharmaceutical products can vary based on the location of the vial inside a freeze dryer. With headspace moisture analysis “wet spots” inside the freeze drier can be identified throughout a lyophilization chamber – on 100% of the samples. This can then be used to optimize freeze drying cycles to obtain a homogenous moisture distribution. Improve your product quality and manufacturing efficiency by eliminating ‘wet spots’ and preventing overdrying of your product.
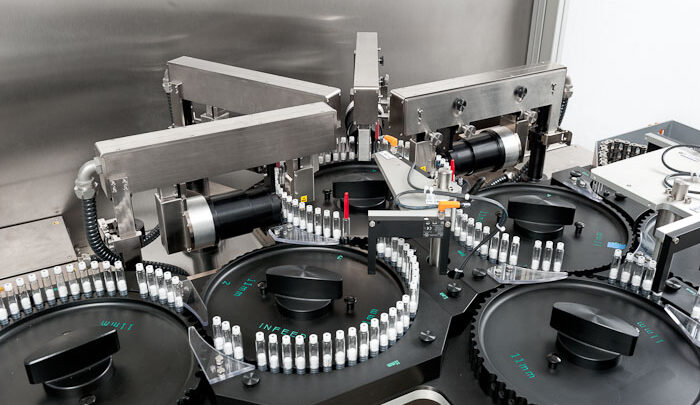
Ensure that no out-of-specification product is released
Non-destructive headspace moisture analysis allows for statistical sampling or 100% inspection of headspace moisture levels for product with a moisture specification. The non-destructive nature of the measurement ensures that no valuable product is lost. More importantly, performing headspace moisture analysis on packaging lines just before labeling ensures that no out of specification product is released to the market.